Understanding the Composition of Rail Car Epoxy
Rail car epoxy is a specialized coating system designed to protect the exterior and interior of train cars from the harsh elements they encounter during operation.
At the heart of this durable solution are epoxy resins, which are known for their exceptional adhesion, chemical resistance, and ability to form a tough, long-lasting film.
The key components of rail car epoxy include:
- Epoxy Resins: These are the primary building blocks of the coating system. Epoxy resins can be formulated using a variety of chemical backbones, each with its own unique properties. Common types used in rail car applications include bisphenol A, bisphenol F, and novolac epoxies, among others. The choice of resin depends on factors such as desired performance characteristics, cure speed, and environmental considerations.
- Hardeners (Curing Agents): Hardeners, also known as curing agents, are responsible for initiating the chemical reaction that transforms the liquid epoxy resin into a solid, cross-linked film. Popular hardener options for rail car epoxy include polyamines, polyamides, and aliphatic amines, each with its own curing profile and impact on the final coating properties.
- Additives: Rail car epoxy formulations may also include a variety of additives to further enhance performance. These can include pigments for color, fillers to improve abrasion resistance, UV stabilizers for weathering protection, and more. The specific additives used depend on the desired application and requirements.
The synergistic interaction of these components is what gives rail car epoxy its exceptional durability, corrosion resistance, and long-lasting protection for the transportation industry.
Chemical Composition Breakdown
Modern rail car epoxy typically consists of:
Component | Purpose | Typical Percentage |
---|---|---|
Epoxy Resin | Base material | 45-55% |
Hardener | Curing agent | 15-25% |
Fillers | Strength enhancement | 15-20% |
Additives | Performance modifiers | 5-10% |
Key Benefits of Rail Car Epoxy
Rail car epoxy coatings offer a versatile and robust solution for protecting the critical components of train cars, delivering a range of benefits that make them an indispensable part of modern railway operations.
Corrosion Resistance
One of the primary advantages of rail car epoxy is its ability to provide unparalleled protection against corrosion. The tough, impermeable film created by the epoxy coating acts as a barrier, shielding the underlying metal from the damaging effects of moisture, chemicals, and environmental exposure.
This corrosion resistance is particularly important for the exterior of rail cars, which must withstand the rigors of harsh weather conditions, road salts, and other corrosive elements during transit.
Durability and Abrasion Resistance
Rail car epoxy coatings are designed to withstand the rigors of heavy-duty use. The cross-linked polymer structure of the cured film provides exceptional durability, resisting chipping, cracking, and peeling even under the most demanding conditions.
Additionally, the inclusion of specialized additives, such as ceramic microspheres or reinforcing fibers, can further enhance the abrasion resistance of the coating, ensuring that it maintains its protective qualities for extended periods.
Chemical Resistance
Rail cars often encounter a wide range of chemicals during their operational life, from spilled cargo to cleaning and maintenance products. Rail car epoxy coatings are formulated to resist a broad spectrum of chemical agents, including acids, alkalies, solvents, and other potentially corrosive substances. This chemical resistance helps to prevent damage to the underlying substrate and maintain the integrity of the coating system.
Ease of Application and Maintenance
Applying rail car epoxy is a relatively straightforward process, with options ranging from manual application methods, such as brushing and rolling, to more efficient spray-on techniques. The inherent versatility of epoxy coatings also allows for easy touch-ups and reapplication as needed, simplifying the maintenance of rail car exteriors and interiors.
Specialized Applications
In addition to the standard exterior and interior coatings, rail car epoxy can be tailored to meet the unique requirements of specialized rail car types. For example, tank cars and hopper cars may require specialized formulations to withstand the specific challenges of their cargo, such as enhanced chemical resistance or increased impact protection.
By leveraging these key benefits, rail car operators can extend the service life of their assets, reduce maintenance costs, and ensure the safe and efficient transportation of goods and materials.
Applications of Rail Car Epoxy
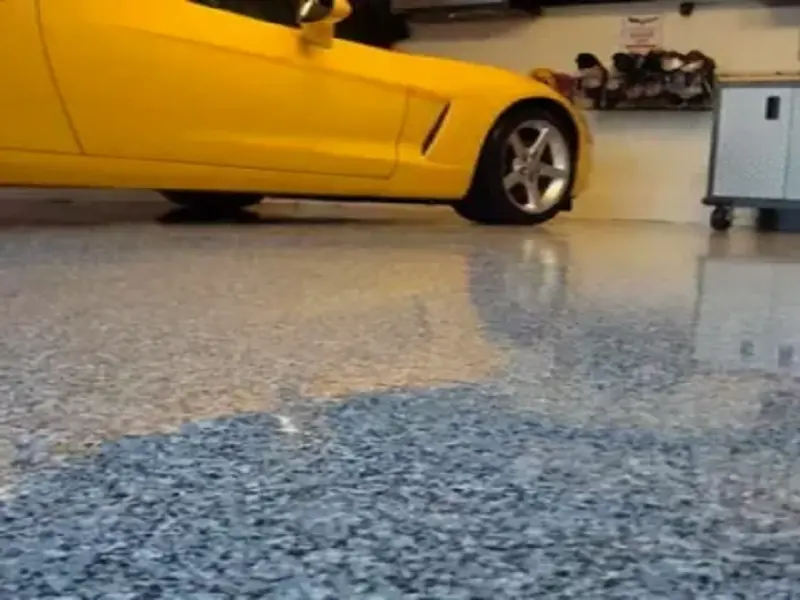
Rail car epoxy coatings find a wide range of applications throughout the transportation industry, providing comprehensive protection for both the exterior and interior of various train car types.
Exterior Coatings
The exterior of rail cars is subjected to a constant barrage of environmental stressors, including weathering, abrasion, and chemical exposure. Rail car epoxy coatings are specifically designed to address these challenges, forming a durable and corrosion-resistant barrier that safeguards the underlying metal components.
Key Exterior Applications:
- Bodywork and undercarriage protection
- Wheel wells and brake components
- Coupling systems and other metal fittings
Interior Coatings
The interior of rail cars also requires specialized protection to maintain cargo integrity and ensure the safety of passengers and crew. Rail car epoxy coatings are well-suited for these applications, offering chemical resistance, easy-to-clean surfaces, and enhanced durability.
Key Interior Applications:
- Cargo containment and storage areas
- Flooring and wall panels
- Tank car linings
- Hopper car coatings
Specialty Applications
In addition to the standard exterior and interior coatings, rail car epoxy can be customized to address the unique requirements of specialized rail car types. These specialized applications often require enhanced performance characteristics to meet the specific challenges presented by the cargo or operating environment.
Specialty Applications:
- Tank car coatings for chemical and hazardous material transport
- Hopper car linings for bulk material handling
- Refrigerated car interior coatings
- Coatings for locomotive engines and components
Regardless of the application, the versatility and performance of rail car epoxy coatings make them an essential component in the efficient and safe operation of modern railway systems.
Surface Preparation and Application Techniques
Achieving the optimal performance and longevity of rail car epoxy coatings requires meticulous attention to surface preparation and the application process. Proper surface preparation ensures the coating’s ability to adhere securely to the substrate, while the application method influences the final film quality and appearance.
Surface Preparation
Before applying rail car epoxy, the substrate must be thoroughly cleaned and pre-treated to create the ideal conditions for the coating to bond effectively.
Key Surface Preparation Steps:
- Cleaning: The surface must be free of any contaminants, such as dirt, grease, rust, or existing coatings. This is typically accomplished through a combination of chemical cleaning, abrasive blasting, or other mechanical means.
- Profiling: The surface is roughened, or “profiled,” to create a mechanical tooth for the epoxy to grip. This can be done through techniques like grit blasting or chemical etching.
- Priming: In some cases, the use of a specialized primer may be required to further enhance the adhesion of the epoxy coating to the substrate.
Proper surface preparation is critical to ensure the long-term performance and durability of the rail car epoxy coating system.
Application Techniques
Rail car epoxy coatings can be applied using a variety of methods, each with its own advantages and suitability for different project requirements.
Common Application Methods:
- Spraying: Airless or conventional spray application is often the most efficient way to apply rail car epoxy, as it can cover large surface areas quickly and evenly.
- Brushing: Manual brushing can be employed for smaller or hard-to-reach areas, as well as for touch-up work.
- Rolling: Roller application is a versatile option that can be used for both interior and exterior coatings.
Regardless of the application method, it is essential to follow the manufacturer’s instructions carefully, paying close attention to factors such as ambient temperature, humidity, and recommended film thickness to ensure a successful and long-lasting application.
Industry Standards and Regulations
The rail transportation industry is subject to a comprehensive set of standards and regulations that govern the use of coatings, including rail car epoxy. These guidelines are in place to ensure the safety, performance, and environmental compliance of all materials used in the construction and maintenance of rail cars.
Transportation Safety Guidelines
Rail car epoxy coatings must meet stringent performance standards set by organizations such as the Association of American Railroads (AAR) and the American Society for Testing and Materials (ASTM). These standards cover a range of criteria, including:
- Flame Spread and Smoke Density: Coatings must demonstrate low flame spread and smoke density to minimize the risk of fire hazards.
- Chemical Resistance: Epoxy coatings must be able to withstand exposure to a variety of chemicals, including fuels, solvents, and cleaning agents.
- Impact and Abrasion Resistance: The coatings must be able to withstand the physical stresses encountered during rail car operations.
Environmental Regulations
In addition to transportation safety, the use of rail car epoxy coatings is also subject to environmental regulations and sustainability considerations. These include:
- Volatile Organic Compound (VOC) Emissions: Epoxy coatings must comply with strict VOC regulations to minimize their environmental impact and ensure worker safety.
- Hazardous Material Handling: The application, storage, and disposal of rail car epoxy coatings must adhere to regulations governing the handling of hazardous materials.
- Sustainability: Manufacturers are increasingly focused on developing eco-friendly epoxy formulations that prioritize sustainability, such as low-VOC or waterborne options.
Compliance with these industry standards and regulations is critical for rail car operators, coating manufacturers, and maintenance providers to ensure the safe and responsible use of rail car epoxy coatings.
Selecting the Right Rail Car Epoxy
Choosing the appropriate rail car epoxy coating for a specific application can be a complex task, as there are numerous factors to consider. Understanding the unique requirements of the project, as well as the performance characteristics of different epoxy formulations, is essential for making an informed decision.
Performance Requirements
The first step in selecting the right rail car epoxy is to identify the specific performance requirements of the application. Key considerations include:
- Corrosion Resistance: The level of protection needed against various corrosive elements, such as chemicals, weathering, and environmental exposure.
- Durability and Abrasion Resistance: The expected lifespan of the coating and its ability to withstand physical stresses.
- Chemical Resistance: The types of chemicals or substances the coating will encounter during its service life.
- Specialized Requirements: Any unique performance needs, such as increased impact protection or thermal resistance.
Epoxy Product Comparison
With the performance requirements in mind, the next step is to evaluate and compare the available rail car epoxy products on the market. Factors to consider include:
- Resin Type: The specific epoxy resin formulation and its impact on overall performance.
- Curing Agent: The type of hardener used and its influence on the coating’s properties.
- Additives: The inclusion of specialized additives, such as reinforcing fibers or UV stabilizers.
- Application Characteristics: Ease of application, film thickness, and drying/curing times.
- Cost and Availability: The overall cost of the epoxy system and its accessibility for the project.
By thoroughly evaluating the performance requirements and carefully comparing the available epoxy products, rail car operators can select the optimal coating solution to meet their specific needs.
Intercoat Adhesion Issues
Common causes and solutions:
Issue | Cause | Solution |
---|---|---|
Delamination | Exceeded recoat window | Mechanical abrasion |
Poor adhesion | Surface contamination | Solvent cleaning |
Pinholes | Improper atomization | Adjust spray pressure |
Maintenance and Repair of Rail Car Epoxy Coatings
Maintaining the integrity and performance of rail car epoxy coatings is crucial for ensuring the long-term protection of these critical transportation assets. Routine inspections, preventive maintenance, and prompt repair of any damage or wear are essential for maximizing the service life of the coating system.
Routine Inspection and Preventive Maintenance
Regular inspections of the rail car epoxy coatings should be a part of the overall maintenance program. These inspections should focus on identifying any signs of wear, damage, or deterioration, such as:
- Cracking, chipping, or peeling of the coating
- Discoloration or fading
- Loss of gloss or surface sheen
- Evidence of corrosion or rust underneath the coating
By addressing any issues identified during these inspections, rail car operators can proactively maintain the protective qualities of the epoxy coatings and extend their service life.
Addressing Wear and Damage
In the event that the rail car epoxy coating does sustain damage, it is essential to address the issue promptly to prevent further deterioration. This may involve:
- Spot Repairs: Small areas of wear or damage can be repaired by thoroughly cleaning the affected region, roughening the surface, and applying a fresh coat of epoxy.
- Full Reapplication: For more extensive damage or when the coating has reached the end of its service life, a full reapplication of the epoxy system may be necessary.
Proper surface preparation and adherence to the manufacturer’s application guidelines are critical to ensure the success of any repair or reapplication efforts.
By implementing a comprehensive maintenance program and addressing any issues in a timely manner, rail car operators can maximize the long-term performance and protection provided by their epoxy coatings.
Emerging Trends and Future Developments
The rail car epoxy industry is continuously evolving, with manufacturers and researchers exploring new advancements to meet the ever-changing demands of the transportation sector. These emerging trends and future developments promise to further enhance the performance, sustainability, and versatility of rail car epoxy coatings.
Advancements in Epoxy Technology
Ongoing research and development in the field of epoxy resins and curing agents are yielding innovative formulations with improved characteristics. Some of the key advancements include:
- High-Performance Epoxy Resins: The development of new resin chemistries, such as novolac and polyester-based epoxies, is leading to coatings with enhanced thermal stability, chemical resistance, and abrasion resistance.
- Environmentally-Friendly Curing Agents: The increased focus on sustainability has prompted the introduction of “green” curing agents, such as bio-based and low-VOC options, to reduce the environmental impact of rail car epoxy coatings.
- Self-Healing Capabilities: Emerging epoxy technologies are exploring the incorporation of microcapsules or other self-healing mechanisms, which can automatically repair minor damage to the coating and extend its service life.
Sustainability and Regulatory Compliance
As environmental regulations continue to tighten, the rail car epoxy industry is responding with a greater emphasis on sustainable and eco-friendly formulations. This includes:
- Low-VOC and Waterborne Epoxy Coatings: Manufacturers are developing water-based and low-VOC epoxy systems that reduce the emission of harmful volatile organic compounds.
- Recycled and Renewable Raw Materials: The use of recycled or bio-based materials in epoxy resin and additive production is becoming more prevalent, improving the overall sustainability of rail car coatings.
- Circular Economy Initiatives: Some manufacturers are exploring ways to facilitate the recycling or reuse of spent rail car epoxy coatings, further enhancing the environmental footprint of these products.
As the rail transportation industry continues to evolve, the advancements in epoxy technology and the drive towards sustainability will play a crucial role in shaping the future of rail car coatings, ensuring they remain an essential component in the safe and efficient movement of goods and passengers.
Cost Analysis & ROI
Investment Breakdown
Average costs per rail car:
Item | Cost Range |
---|---|
Materials | $3,000-4,500 |
Labor | $5,000-7,000 |
Equipment | $800-1,200 |
Total | $8,800-12,700 |
Conclusion
Rail car epoxy coatings have become an indispensable part of the modern transportation industry, providing unparalleled protection and extending the service life of these critical assets.
By understanding the composition, benefits, and application of these specialized coatings, rail car operators can make informed decisions to safeguard their investments and ensure the safe and efficient movement of goods and passengers.
As the industry continues to evolve, with advancements in epoxy technology and a growing emphasis on sustainability, the role of rail car epoxy coatings will only become more significant.
By staying attuned to these developments and maintaining a proactive approach to coating selection and maintenance, rail car operators can unlock the full potential of these durable and versatile solutions, contributing to the overall success and reliability of the transportation network.
Frequently Asked Questions About Rail Car Epoxy
1. What makes rail car epoxy coatings so durable?
Rail car epoxy coatings are renowned for their exceptional durability due to the inherent properties of the epoxy resin system. The cross-linking that occurs during the curing process creates a tough, abrasion-resistant film that can withstand the rigors of heavy-duty rail car operations. Additionally, the inclusion of specialized additives, such as reinforcing fibers or ceramic microspheres, further enhances the coating’s ability to resist wear, impact, and other physical stresses.
2. How do rail car epoxy coatings protect against corrosion?
The key to the corrosion resistance of rail car epoxy coatings lies in their ability to form a dense, impermeable barrier that shields the underlying metal from exposure to moisture, chemicals, and other corrosive elements. The epoxy resin system effectively seals the surface, preventing the penetration of these harmful substances and maintaining the integrity of the rail car’s structure.
3. Can rail car epoxy coatings be easily repaired or reapplied?
Yes, rail car epoxy coatings can be readily repaired or reapplied as needed. For small areas of wear or damage, spot repairs can be made by thoroughly cleaning the affected region, roughening the surface, and applying a fresh coat of epoxy. In cases of more extensive damage or when the coating has reached the end of its service life, a full reapplication of the epoxy system can be undertaken, following the manufacturer’s recommended surface preparation and application guidelines.
4. How do rail car epoxy coatings comply with industry standards and regulations?
Rail car epoxy coatings must meet stringent performance standards set by organizations such as the Association of American Railroads (AAR) and the American Society for Testing and Materials (ASTM). These standards cover a range of criteria, including flame spread, smoke density, chemical resistance, and physical durability. Additionally, the coatings must comply with environmental regulations governing volatile organic compound (VOC) emissions and the handling of hazardous materials.
5. What are some of the emerging trends in rail car epoxy coatings?
The rail car epoxy industry is continuously evolving, with manufacturers and researchers exploring new advancements to meet the ever-changing demands of the transportation sector. Some of the emerging trends include the development of high-performance epoxy resins, the introduction of environmentally-friendly curing agents, the incorporation of self-healing capabilities, and the focus on sustainable and eco-friendly formulations with reduced VOC emissions and the use of recycled or renewable raw materials.

With over 5 years of dedicated experience in the automotive industry, I am passionate about all things automotive. My journey began with a deep curiosity for automobiles, which led me to delve deeper into their mechanics, technology and trends. My expertise spans various aspects of the automotive world, from the latest electric vehicles to classic car restoration techniques. Through my articles, I aim to share my knowledge and insights, helping readers stay informed and inspired in the fast-paced world of the automobile.